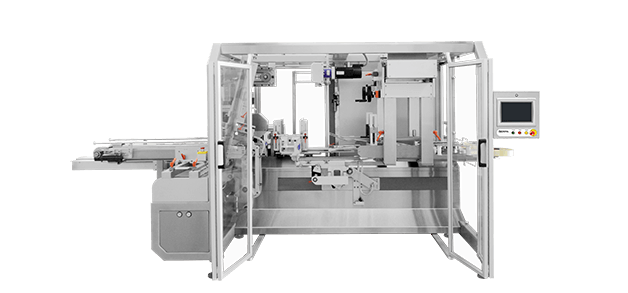
For most consumer packaged goods (CPG) companies, fierce competition and tight margins are facts of life. These companies need to get the most out of every investment — and that includes their packaging equipment. Performance, reliability, and fast changeover times are all factors in choosing the right packaging solution.
But there’s another attribute — versatility — that makes a big difference for many CPG companies. A packaging machine that can easily switch between different lines and products can maximize usage and eliminate the need for multiple machines. That’s why the Serpa P200 Side Load Case Packer has become one of our most popular packaging solutions.
Flexibility to Handle Multiple Product Lines
The side-load P200 is designed to package a wide range of products into cases or trays. This flexibility allows companies to maximize machine usage. For example, a company with a packaging line that produces bottles and cartons, each running at 45% capacity, would typically need to run two separate machines. Using the P200, the company could run both products on a single machine operating at 90% capacity.
Eliminating a packaging machine represents a tangible capital cost savings, frees up valuable floor space, and reduces operator workforce requirements.
Engineered to Reduce Jamming
Die-cut cases are glued together at the joints, which can cause significant variations from case to case. Traditional packaging machines transport cases using a lug chain that has a low tolerance for these variations. As a result, lug chain systems are prone to jamming, creating downtime as the operator must shut down the machine and remove the affected items.
The P200 uses a more forgiving ‘walking beam’ design that can accept wider variances than traditional machines. Less operator intervention is required to adjust for case variations, allowing the P200 to deliver more uptime.
If a jam does occur, the P200 incorporates Serpa’s ‘Easy Case Clear Out’ feature. The open design of the P200 offers complete operator access to the closing area. When clearing a jam, the entire closing section slides open without impacting changeover points or other system settings.
Full Walk-In Access
The P200 is built with a ‘walk-in’ design that provides an operator full access to the machine’s operational areas. By simply sliding the bi-fold doors open, the operator can safely enter — there is nothing to step on or trip over. If a jam does occur in the load area or closing section, it can be easily cleared from the machine’s operator side.
This walk-in feature can dramatically reduce the time it takes to correct a product jam. While clearing a jam in a traditional system may mean a half-hour of downtime, the same task typically takes just a few moments with the P200.
This enhanced accessibility also allows maintenance to be conducted swiftly and safely — another way the P200 can minimize downtime.
Faster Changeovers
As the P200 is designed to handle a wide range of product packaging requirements, completing changeovers must be quick and straightforward. Traditional machines often require precise and time-consuming lug adjustments, and a typical changeover can take 30-60 minutes.
Changeover adjustments are tool-less on the P200 through rotary dials and Kipp handles for linear adjustments. Additionally, the P200 uses minimal change parts to complete changeovers.
As a result, changeovers with the P200 can often be accomplished in as little as 5 minutes — much less time than with other industry solutions.
Versatile, Compact, and Cost-Effective
“We chose the P200 for its craftsmanship, reliability, and the speed of the line. Our experience with the Serpa team has been great from start to finish.”
—Maintenance Supervisor, a leading CPG company
Like the fabled Swiss army knife, the P200 is a flexible solution for many packaging requirements. It can run a multitude of products, from bottles to cartons to bundles, with loading into side or end load cases and trays. The P200 is ideal for any industry’s application.
The P200 offers a fall-through construction for easy cleaning and is available in stainless steel, meeting all sanitary and FDA validation requirements.
A compact footprint means the P200 makes the best use of valuable floor space, and the belt drive design promises less maintenance and a longer lifespan than chain-driven machines.
The return on investment, however, is where the P200 stands out. A single P200 can often take the place of multiple machines, preserving capital and lowering operating expenses. Greater reliability, fewer jams, and faster changeovers all combine to provide industry-leading uptime and higher production efficiency.
At Serpa, we’ve built the P200 to be the most versatile packaging solution available — no matter what the package.