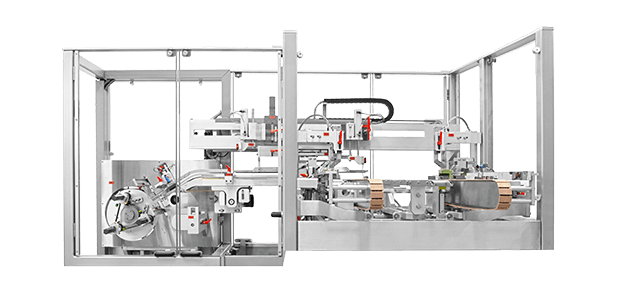
At Serpa, we’re always listening to our customers to find ways to improve their productivity and profitability. Many of our customers have reported ongoing challenges with their friction feeder systems. In response, we created a new, high-speed insert feeding system that integrates two machines to eliminate the well-known limitations of conventional gravity-fed friction feeder systems. In late 2019, Serpa received a patent for this innovative new solution.
The Problem with Friction Feeders
Pharmaceutical companies and other CPG firms often include leaflets or other literature in their product packages. Most traditional packaging machines use gravity-fed friction feeders to load these leaflets. These legacy systems have two well-known weaknesses, however, that often lead to downtime and reduced productivity.
Jamming. Friction feeders rely on a vertical gravity stack to advance each leaflet into the correct package insertion position. Any variation in leaflets loaded in the gravity stack (such as an imprecise cut or fold) can cause a twist or jam in the friction feeder, and the machine must be taken offline to be dismantled, cleared, and reset. This downtime can occur several times a shift — and it quickly adds up.
Frequent Loading. Operators must load leaflets into trays, which then supply the gravity-fed friction feeder. In high-speed applications, these trays sometimes need to be loaded every 30 seconds, requiring a dedicated operator to complete the task.
Serpa’s patented high-speed insert feeding system combines two machines, the RF450 and the TL450, to eliminate jamming and reduce loading frequency. For customers, this means less downtime and lower operating costs.
The Serpa RF450 — Say Goodbye to Leaflet Jams
While legacy systems rely on gravity-feeding and friction, Serpa’s RF450 employs a rotary style, vacuum ‘pick and place’ system. Using live tabbing on the leaflets, the RF450 separates each leading leaflet and presents it to the vacuum pick head. The solution also incorporates a clamp mechanism to provide constant back pressure on the leaflet stack, keeping all leaflets securely in place as they go through the loading cycle. Leaflets are driven continuously throughout the process, and there are no vertical troughs that rely on gravity to drop the leaflets onto a belt.
As a result, the RF450 delivers high-speed insertion capabilities (400+ PPM) with virtually no leaflet jamming or twisting issues. The resulting increase in uptime provides a measurable, and, in some cases, dramatic improvement in productivity.
The Serpa TL450 — Less Operator Intervention Drives Labor Savings
Even when running smoothly and at capacity, traditional friction feeders have to be manually loaded by an operator— in some cases, almost continuously. Dedicating an operator to this single task represents a considerable expense to the entire packaging operation.
Serpa’s TL450 provides an elegant solution to this loading challenge. With the TL450, operators load multiple leaflet trays into an accumulation area. As the feeder magazine becomes depleted, the TL450 ‘walks’ a new tray into the magazine, providing an uninterrupted leaflet flow.
While some other feeders incorporate accumulation-type systems, these typically rely on a ‘waterfall effect’ which requires leaflets to fall precisely into place at high speeds. This creates another potential jamming point.
The TL450 doesn’t employ a ‘waterfall’; instead, it keeps all leaflets on edge and maintains back pressure throughout the entire cycle, eliminating another trouble-spot.
The system also minimizes potential problems caused by errant leaflets by providing front and back tray containment and keeping constant back pressure on the leaflets in the magazine as the new full tray is loaded.
Using the TL450 can have a significant impact on operator productivity. In one application, a pharmaceutical customer was able to achieve almost one hour of run-time without operator intervention, freeing up the operator to perform other critical tasks on the line.
Designed for Flexibility and Quick Changeovers
Eliminating feeder jams isn’t the only way the Serpa high-speed insert feeding system improves uptime. The solution can accommodate a wide range of printed materials and is much faster to set up and change over compared to traditional systems.
Many of the mechanisms within our solution are tied together, simplifying and reducing the number of adjustments required during changeover. Unlike conventional systems, the Serpa machine doesn’t require priming with leaflets at set-up.
As a result, the Serpa system can typically be changed over in five minutes or less, maximizing run-time and productivity.
Built to Deliver Greater Productivity and a Better ROI
By integrating the RF450 and the TL450 into a single solution, Serpa’s newly-patented high-speed feeding system delivers measurable benefits to many of our customers.
Minimizing or eliminating feeder jams can add precious minutes of run-time every day. Simple, consistent changeovers that can be completed in as little as five minutes also boost uptime.
Reducing operator loading requirements can also deliver significant savings. In some cases, a previously dedicated operator may only need to load the solution every hour. This may, in effect, ‘give back’ 75% or more of that operator’s time to perform other functions.
As with all of our solutions, we created the Serpa high-speed feeding system based on feedback from our customers. It’s designed to provide an innovative solution to a real customer challenge — with an eye to improving our customers’ bottom line.